The Scientific Research Behind Porosity: A Comprehensive Guide for Welders and Fabricators
Understanding the elaborate systems behind porosity in welding is vital for welders and makers making every effort for impressive workmanship. As metalworkers delve right into the midsts of this sensation, they discover a globe regulated by different aspects that influence the formation of these small voids within welds. From the composition of the base materials to the intricacies of the welding procedure itself, a plethora of variables conspire to either exacerbate or reduce the existence of porosity. In this extensive guide, we will unravel the science behind porosity, exploring its effects on weld top quality and introduction progressed techniques for its control. Join us on this journey via the microcosm of welding imperfections, where precision fulfills understanding in the search of remarkable welds.
Understanding Porosity in Welding
FIRST SENTENCE:
Exam of porosity in welding exposes critical insights right into the integrity and high quality of the weld joint. Porosity, identified by the existence of dental caries or voids within the weld steel, is an usual issue in welding procedures. These voids, if not appropriately addressed, can jeopardize the architectural integrity and mechanical properties of the weld, resulting in possible failures in the ended up item.

To find and evaluate porosity, non-destructive screening methods such as ultrasonic testing or X-ray assessment are usually employed. These techniques enable for the identification of interior issues without endangering the integrity of the weld. By evaluating the size, shape, and distribution of porosity within a weld, welders can make educated decisions to enhance their welding processes and attain sounder weld joints.
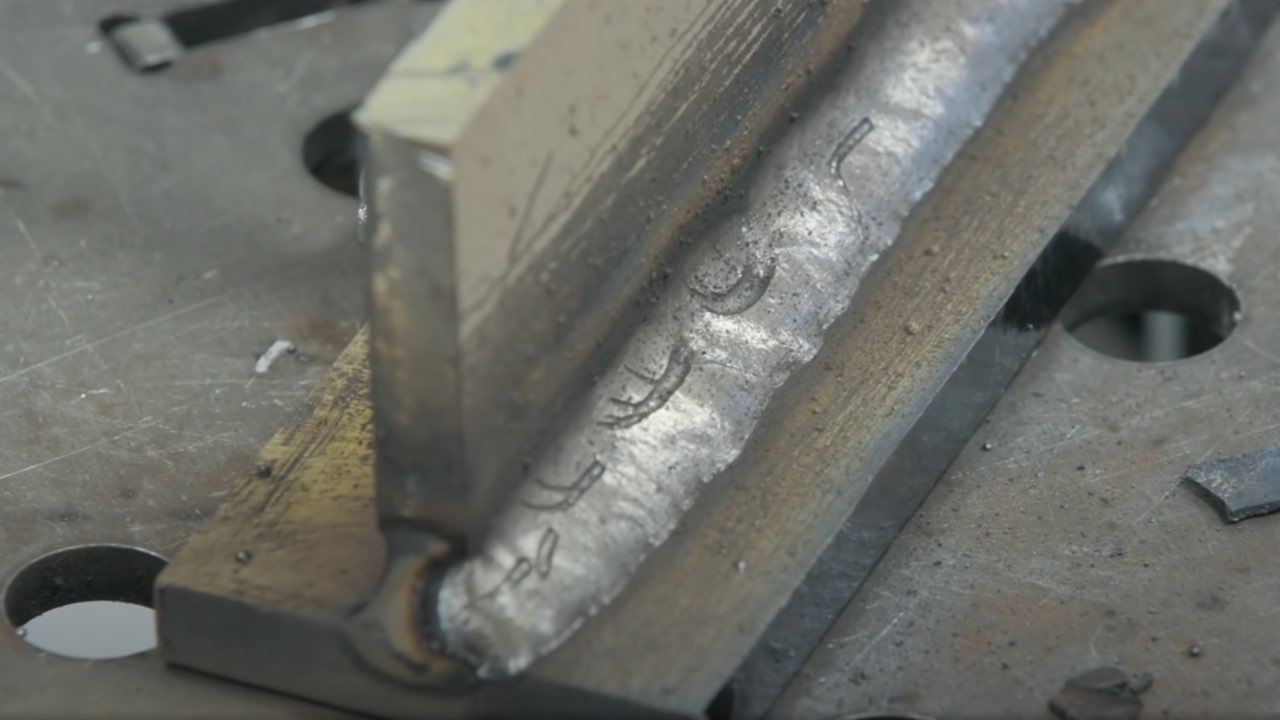
Aspects Affecting Porosity Development
The event of porosity in welding is influenced by a myriad of aspects, varying from gas protecting efficiency to the ins and outs of welding criterion setups. One critical variable adding to porosity development is poor gas securing. When the securing gas, commonly argon or carbon dioxide, is not successfully covering the weld pool, atmospheric gases like oxygen and nitrogen can contaminate the liquified steel, bring about porosity. In addition, the tidiness of the base materials plays a significant role. Pollutants such as corrosion, oil, or dampness can vaporize throughout welding, developing gas pockets within the weld. Welding parameters, consisting of voltage, existing, take a trip rate, and electrode kind, likewise impact porosity development. Making use of inappropriate setups can generate excessive spatter or warmth input, which consequently can result in porosity. In addition, the welding strategy utilized, such as gas metal arc welding (GMAW) or secured metal arc welding (SMAW), can influence porosity development because of variants in warm distribution and gas insurance coverage. Understanding and regulating these aspects are vital for lessening porosity in welding operations.
Effects of Porosity on Weld High Quality
The existence of porosity likewise compromises the weld's resistance to deterioration, as the entraped air or gases within the gaps can respond with the surrounding atmosphere, leading to deterioration over time. Additionally, porosity can hinder the weld's capacity to endure pressure or impact, more threatening the general quality and reliability of the bonded structure. In essential applications such as aerospace, auto, or architectural constructions, where safety and security and longevity are vital, the harmful effects of porosity on weld high quality can have severe effects, highlighting the significance of minimizing porosity with proper welding strategies and treatments.
Methods to Minimize Porosity
To boost the high quality of bonded joints and make sure structural honesty, welders and fabricators use certain techniques discover here focused on reducing the development of voids and dental caries within the product during the welding procedure. One efficient approach to reduce porosity is to make certain appropriate product preparation. This includes comprehensive cleansing of the base metal to eliminate any kind of pollutants such as oil, oil, or moisture that might contribute to porosity formation. In addition, using the proper welding criteria, such as the appropriate voltage, existing, and take a trip speed, is vital in stopping porosity. Keeping a consistent arc length and angle throughout welding additionally helps in reducing the likelihood of porosity.

Using the appropriate welding technique, such as back-stepping or using a weaving activity, can likewise help disperse warm evenly and lower the opportunities of porosity formation. By executing these strategies, welders can properly lessen porosity and produce high-quality bonded joints.
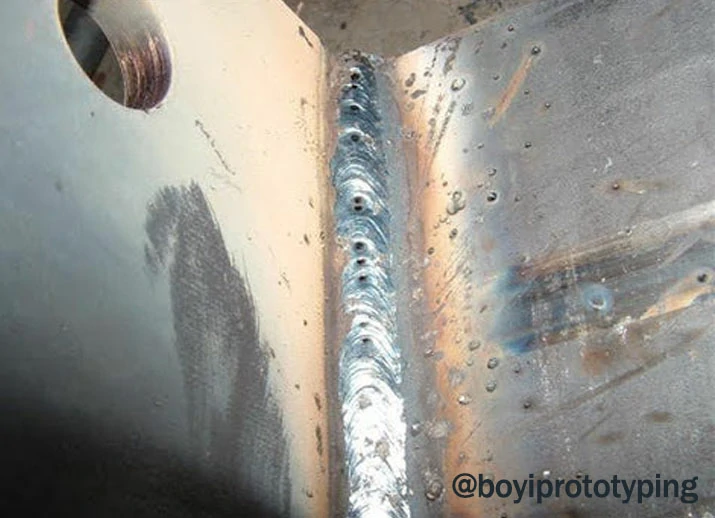
Advanced Solutions for Porosity Control
Applying sophisticated innovations and ingenious methods plays a crucial duty in accomplishing superior control over porosity in welding procedures. One advanced service is the use of sophisticated gas combinations. Protecting gases like helium or a mixture of argon and hydrogen can help in reducing porosity by giving much better arc security and enhanced gas coverage. Furthermore, employing advanced welding strategies such as pulsed MIG welding or modified ambience welding can also aid reduce porosity concerns.
One more sophisticated remedy involves using innovative welding tools. As an example, using tools with integrated features like waveform control and advanced source of power can improve weld top quality and reduce porosity dangers. The implementation of automated welding systems with accurate control over specifications can substantially decrease porosity issues.
In addition, incorporating advanced monitoring and inspection technologies such as real-time X-ray imaging or automated ultrasonic testing can assist in spotting porosity early in the welding process, enabling for instant corrective actions. Overall, incorporating these innovative options can substantially enhance porosity control and enhance the overall top quality of bonded elements.
Conclusion
In final thought, understanding the science behind porosity Homepage in welding is essential for welders and makers to produce high-grade welds - What is Porosity. special info Advanced options for porosity control can further improve the welding procedure and guarantee a solid and dependable weld.